Metal Electroplating Services
- Home
- Metal Electroplating Services

ZINC- NICKEL ELECTROPLATING
Zinc-Nickel is a high performance coating that offers exceptional corrosion resistance particularly for parts used in harsh environments.
Alloying Nickel with Zinc creates a unique composition that will approximately 10-15% nickel and the remainder zinc, this alloy coating can provide up to ten times the protection of conventional zinc plating.
There is an increasing demand across industries for the high-corrosion resistance of Zinc-Nickel due to factors such as extended product warranties, longer life cycle requirements, more stringent safety standards and reduction of environmental impact.
ACID ZINC ELECTROPLATING- HEXAVALENT
Acid Zinc Electroplating Services procedure is performed using acid zinc that has good broad mindedness to high temperature & electrical energy, hence, ideal to be used in barrel and rack zinc plating.
Besides, our better quality Acid Zinc Plating Process is a dependable and produced exceptionally bright leveled & ductile zinc good tolerance.
This process complies with the international standards, used in barrel and rack zinc plating.
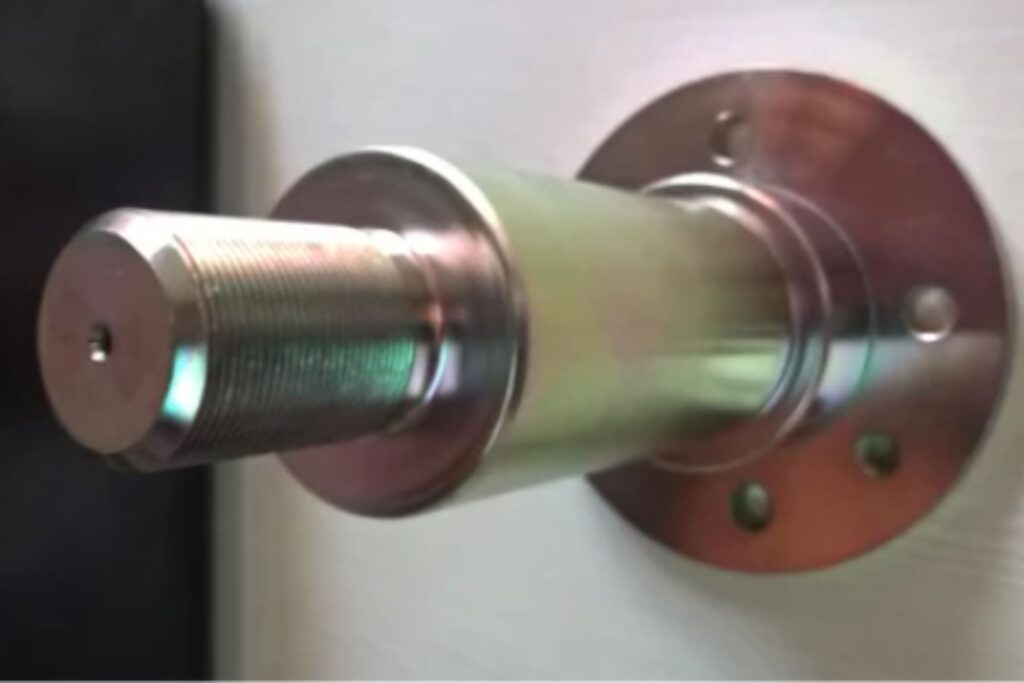
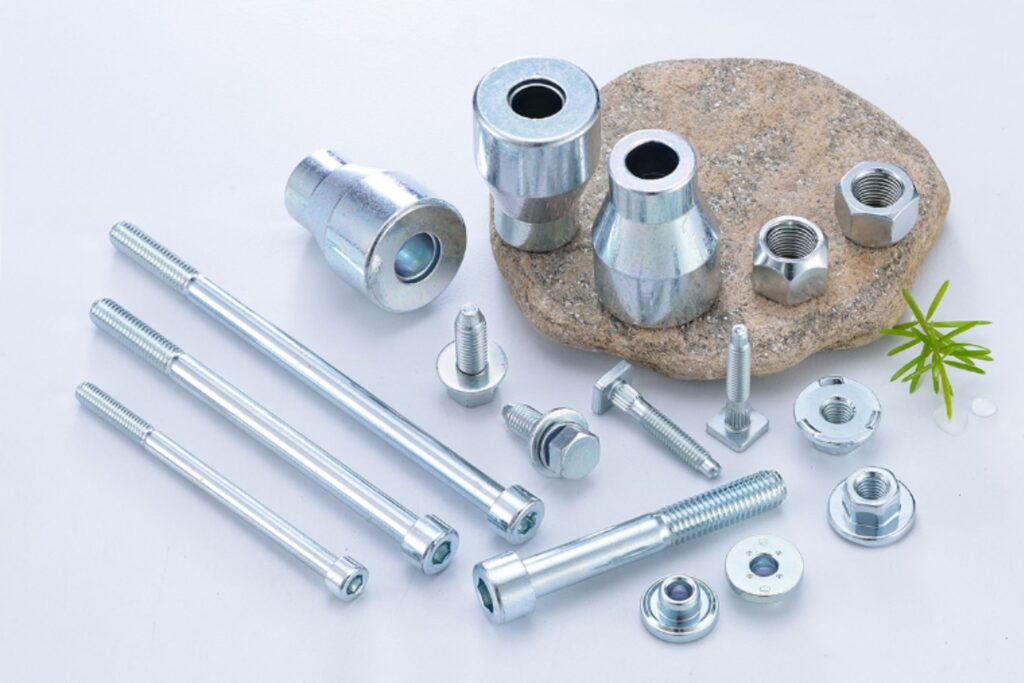
ZINC ELECTROPLATING WITH TRIVALENT PASSIVATIONS
To fulfill the demands and requirements of our prestigious customers, we undertake Surface Coating Services.
We render all our services utilizing latest technology and instruments along with premium raw material, which is sourced from the reliable vendors of the market.
These services are widely demanded by the customers due to their reliability, cost-effectiveness, timely execution and flexibility.
MANGANESE PHOSPHATE COATING SERVICES
We are able of render excellent Manganese phosphate coating services. Widely demanded by automobile industry, our services are executed using high-grade raw material and advanced tools and instruments. During the execution of undertaken project, our expert professionals incorporate even the minute detail given by the customers to achieve their utmost satisfaction. We offer manganese phosphate coating to shafts and hollow shafts up to 900 mm length with controlled thickness. The phosphate coatings need not stand for an extended length of time, because it is in the initial movements, that parts can be damaged and require lubricity eg. scoring of gears usually takes place in the first few revolutions, during this time, phosphate coating prevents intimate contact of the faces.
As the coating broken down in the operation, some of it is packed into pits or small cavities formed in the mating surfaces by the etching action of the acid during phosphating. Long after break-in, this material packed into the pits prevents direct contact of mating surfaces.
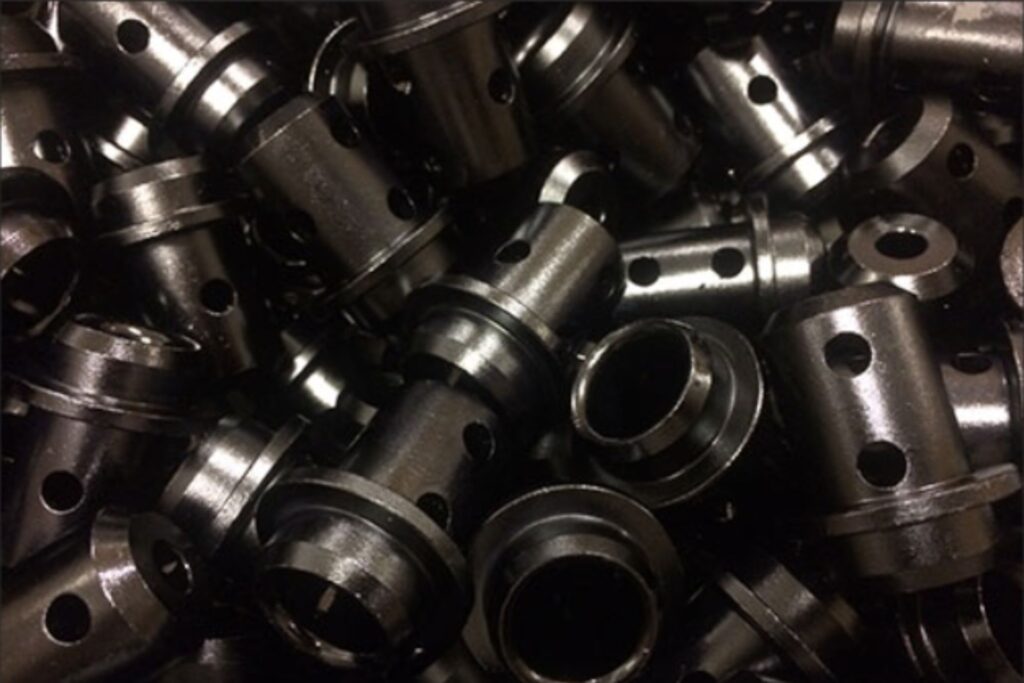
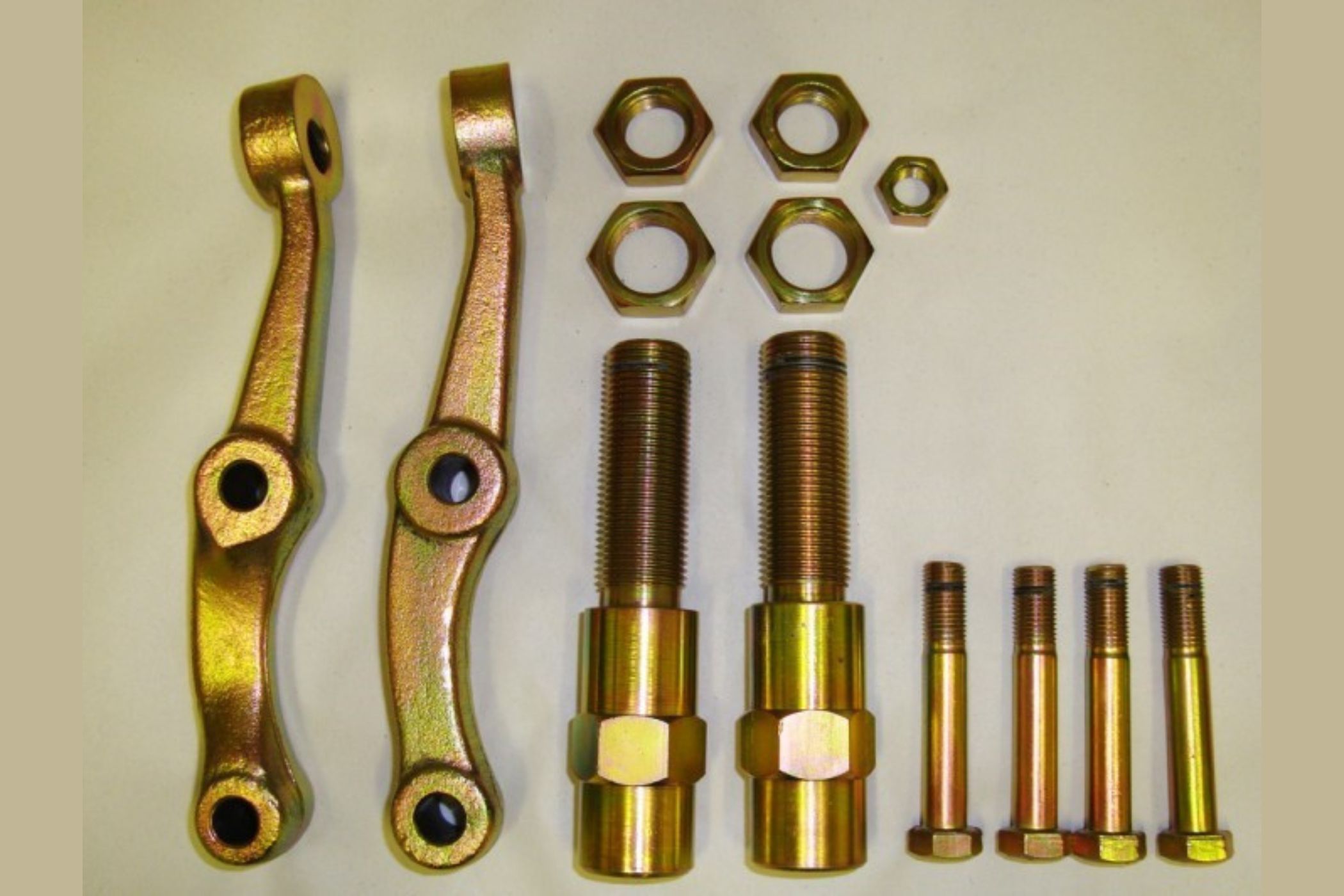
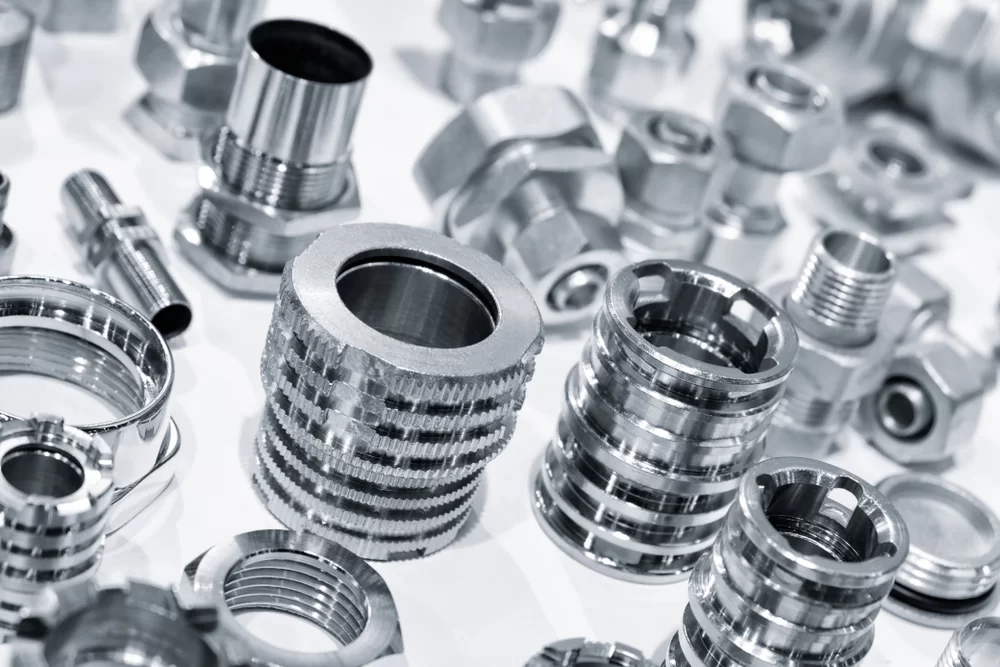
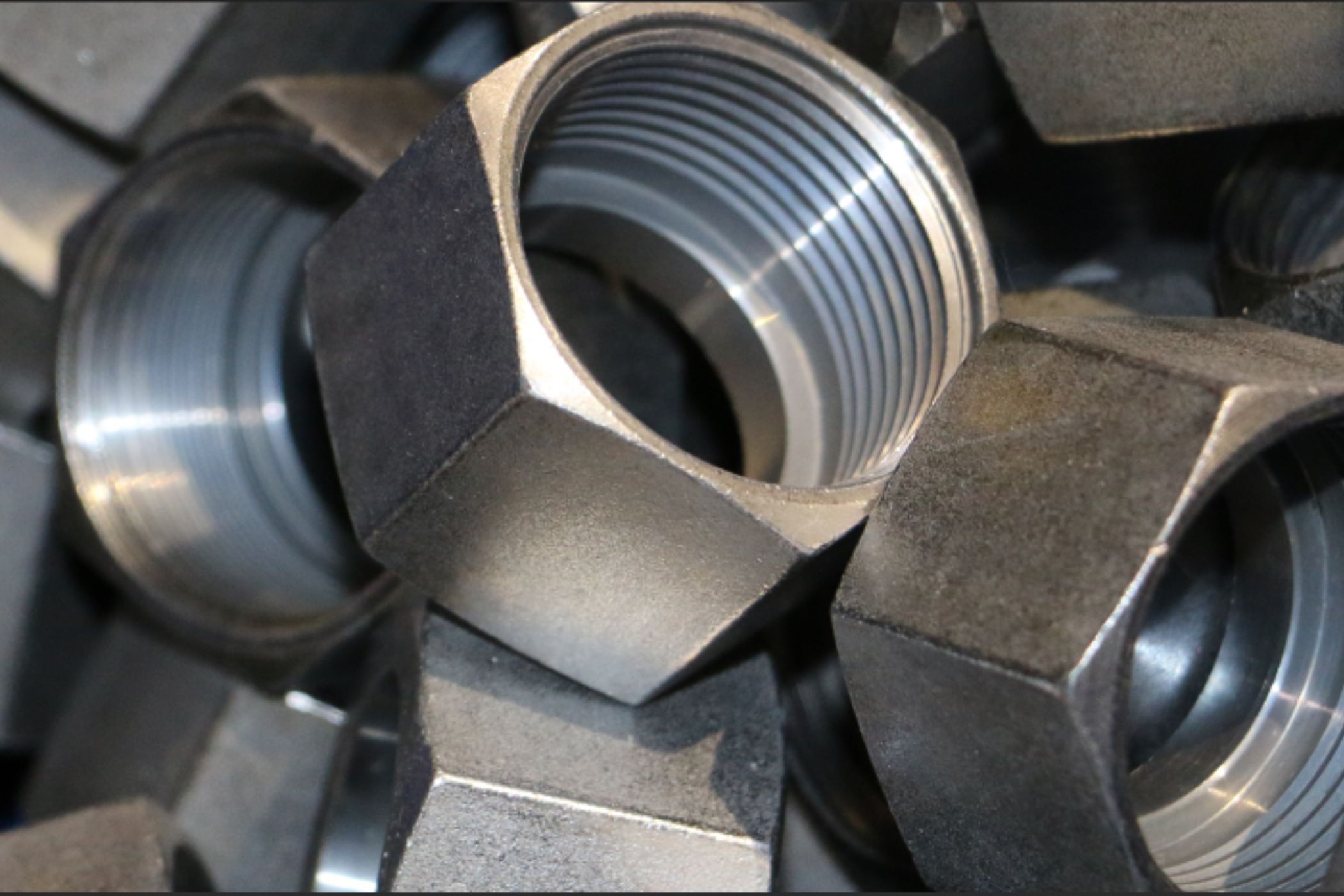
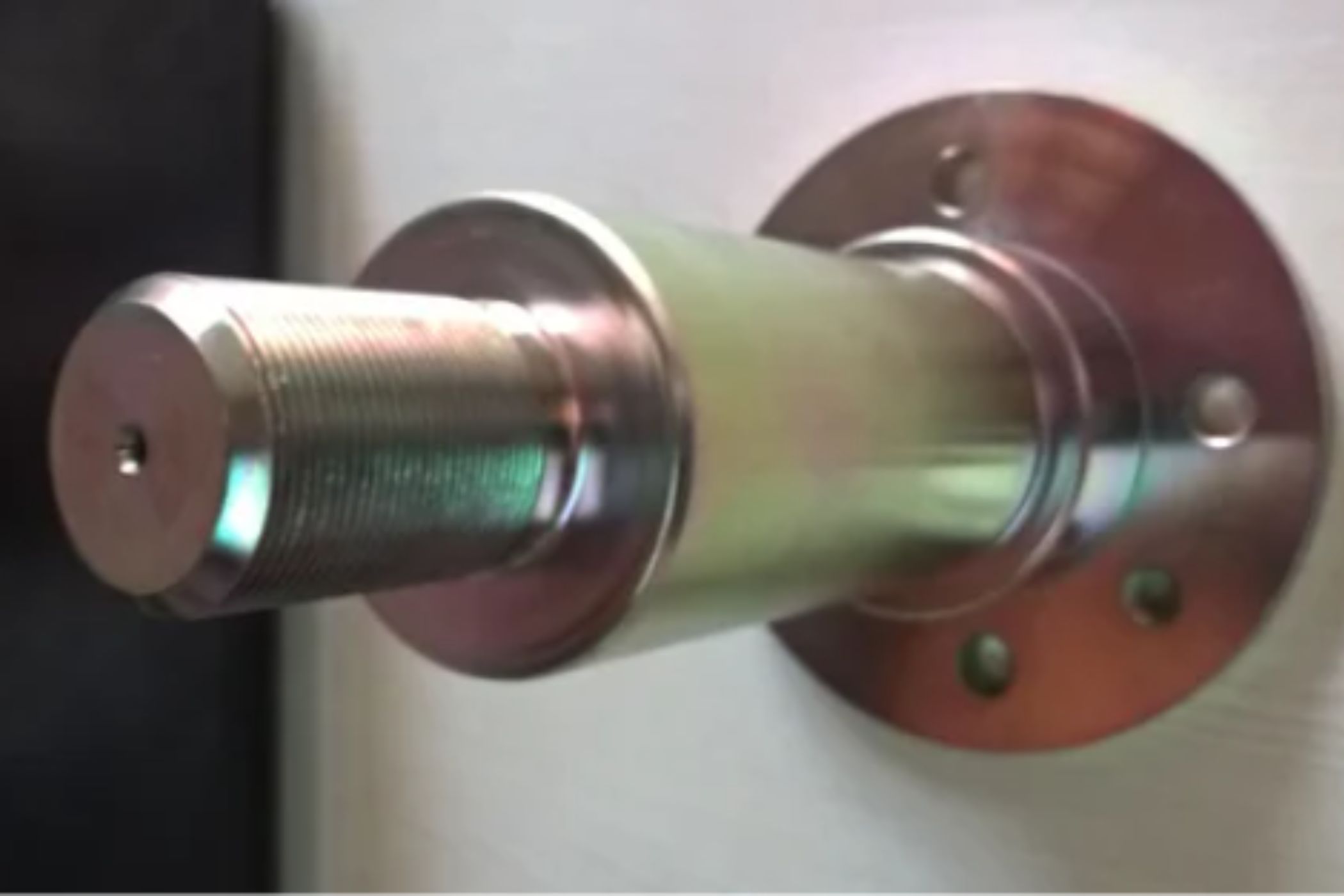
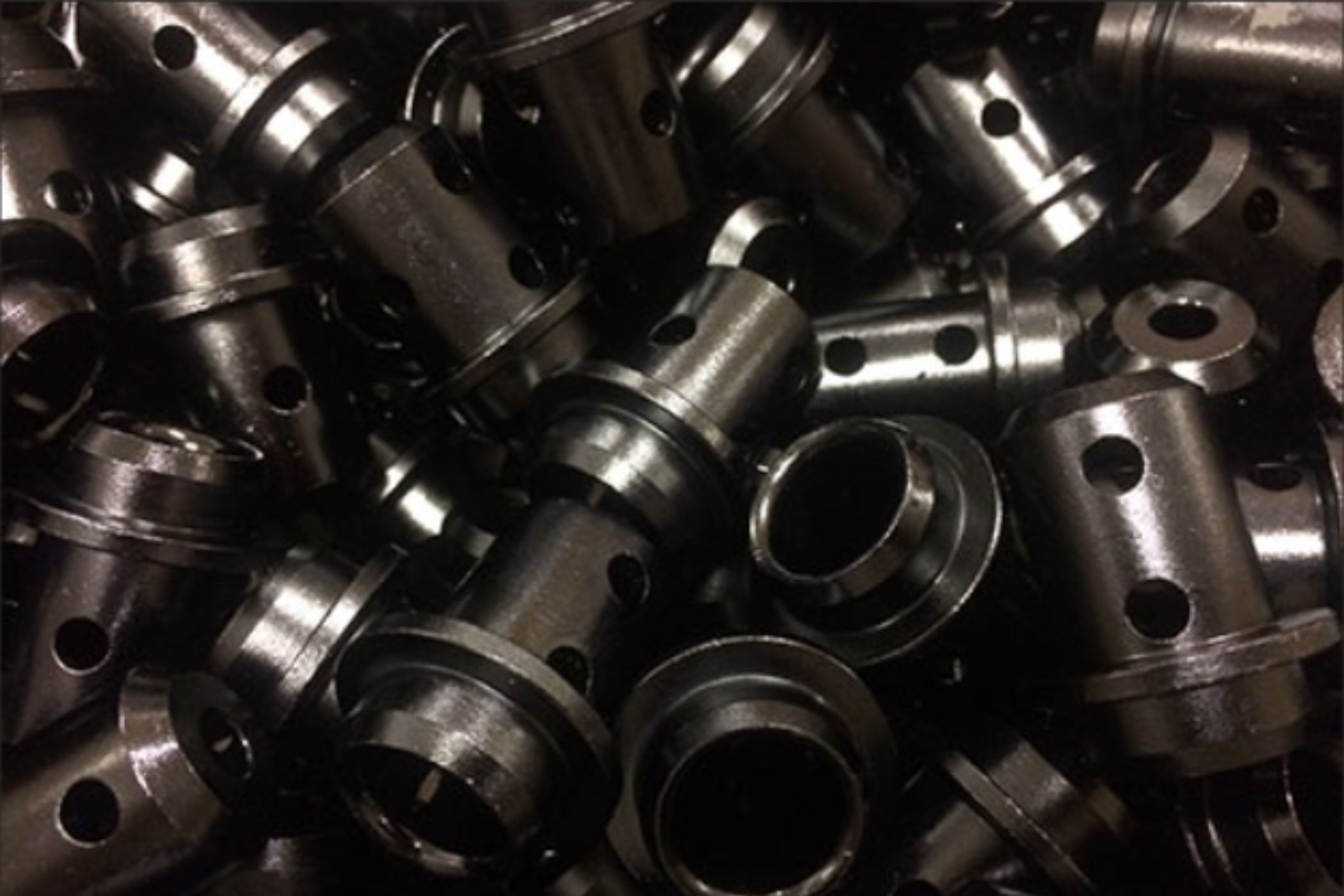
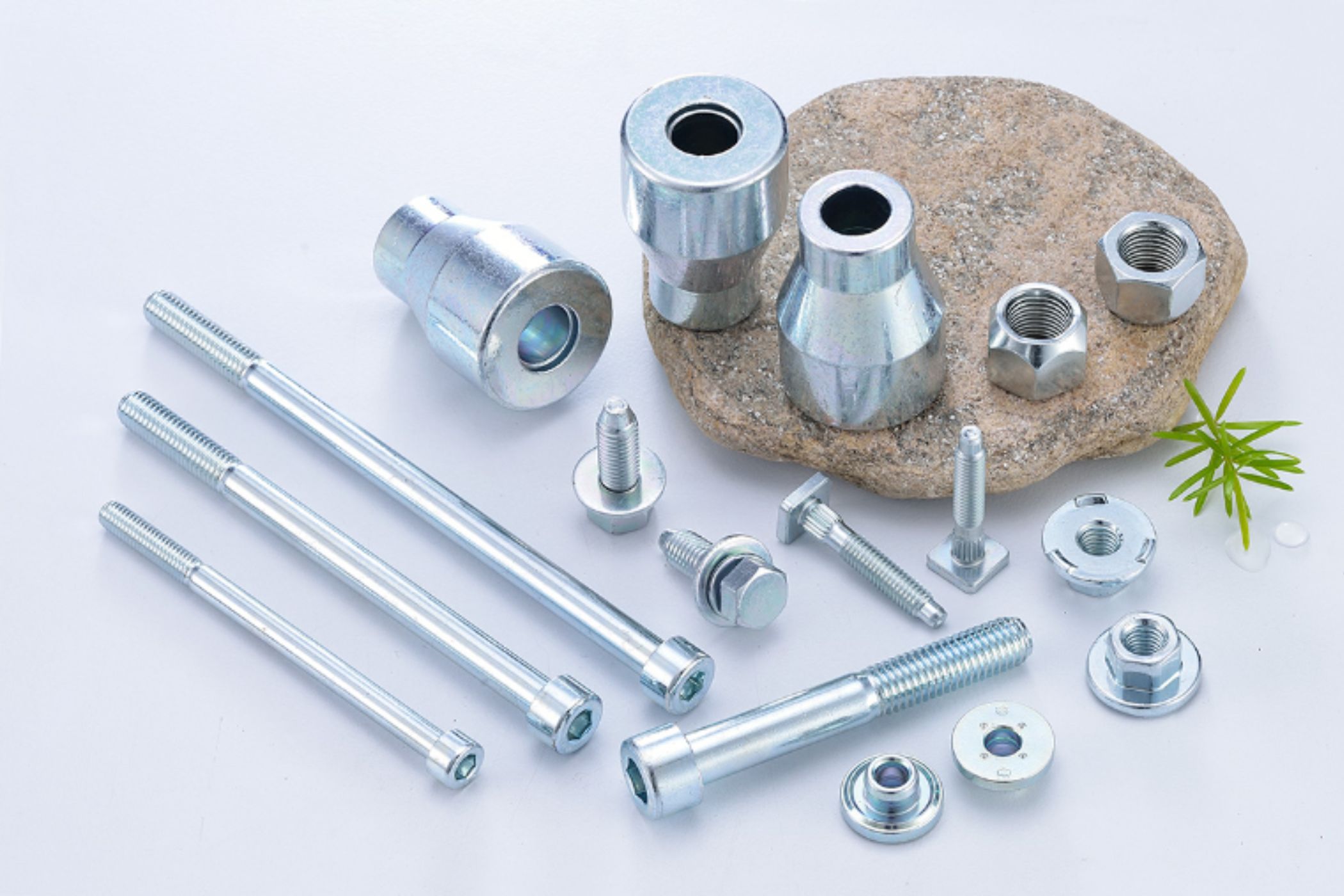